How to use water-borne coatings for metal treatment and protection
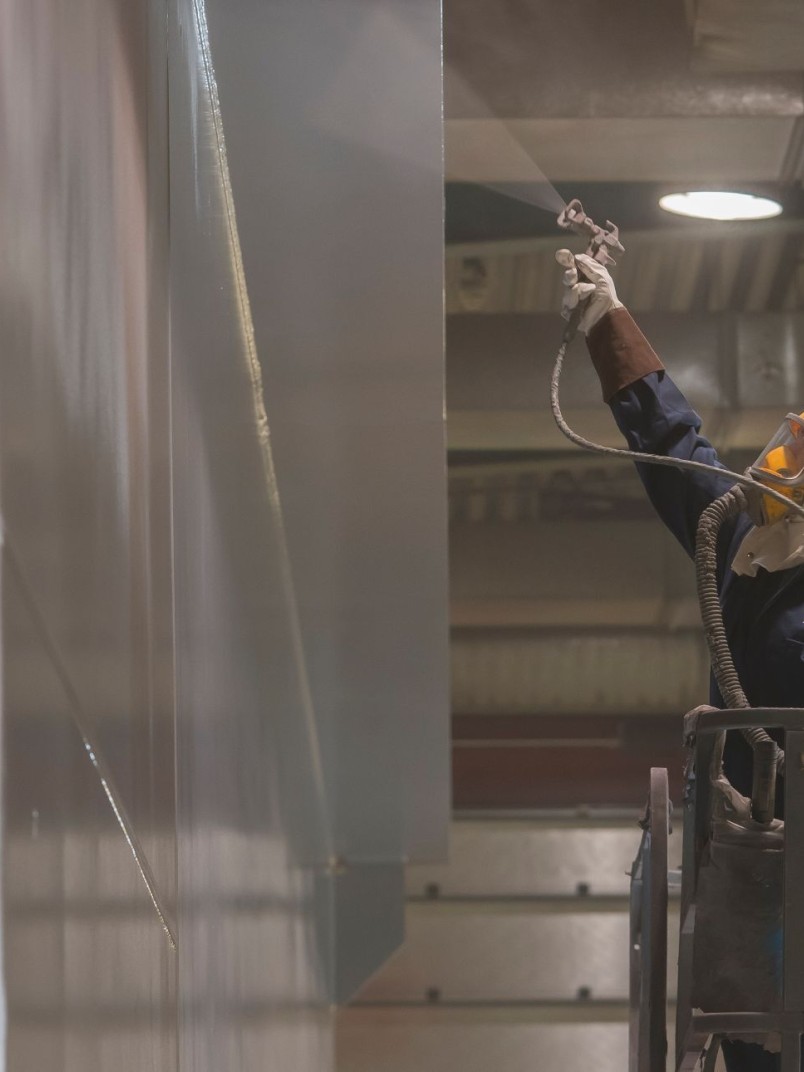
How should you work with water-borne industrial metal coatings to achieve the best possible results? Keep reading for expert tips for working with these products—from choosing the right products to maintaining your coatings.
Decide what type of water-borne products you need
How can you choose the right water-borne paints for your business? When looking into different water-borne primers, topcoats, direct-to-metal (DTM), or lacquers, consider the following factors:
- The types of metals you’re working with
- Where and how your end product is used
- The painting conditions you’re working with
- Whether you paint or assemble first
- How long you need the paint to hold
- The painting system standards you need to comply with
- Your current processes
- What drying time you need
- How much you should be able to paint in one day
At Tikkurila, our water-borne products for metal surfaces fully comply with exacting industrial quality standards and the latest environmental regulations. Some of our water-borne coatings can be used as a direct-to-metal (DTM) system, which reduces your production costs.
Use the right equipment
With water-borne coatings, you need equipment with non-rusting metals in all parts that are in contact with wet water-borne paint. You’ll use different equipment and techniques for paint application, maintenance and drying. Since water-borne paint isn’t flammable, you don’t need any special explosion-proof equipment, which can help you cut costs.
Clean and prepare the surface material
Surface preparation has a huge impact on the success of your metal coatings treatment. While solvent-borne coatings are more forgiving of surfaces with traces of dirt of grease, water-borne coatings require a completely clean environment and surface. Since these paints don't tolerate any grease or oil on the surface, cleaning needs to be to the highest standard.
With pre-cleaning, first remove any dirt, dust, soluble salts, and other impurities. Then clean any grease away before using blast cleaning to remove rust from the surface. Blast cleaning also ensures proper paint adhesion. Since rust forms quite easily onto plain steel surfaces, this cleaning must be done just before painting.
When applying water-borne paint on steel surfaces, you can degrease and blast clean to grade Sa2½ (ISO 8501-1). If blast cleaning is not possible, phosphating is recommended for cold rolled steel to improve adhesion. Phosphating also improves the corrosion durability of the painted surface.
For primed surfaces, first remove oil, grease, salt, and dirt from the surface, then repair any damage to the primer coat. Make sure to check your product's data sheet for guidance regarding previously primed surfaces.
Apply the water-borne paint correctly
Only after proper surface preparation, you can apply the water-borne paint to the metal surface. To ensure the best possible results and improve the water-borne metal coating’s performance lifetime, be precise and clean throughout this process. When applied correctly, water-borne metal coatings give you a smooth, long-lasting finish.
The best application methods for water-borne paint depend on a few factors including:
- The water-borne product you’re using
- Your equipment
- Your production speed
- Your output speed
- Whether you’re applying at the painting shop or at a different location
There are several different types of equipment you can use to apply water-borne paint. Spraying is the most popular application technique, but you can also use dip coating. Application robots are especially good for narrow spaces and when you need a consistent, high-quality finish.
Automatic spray equipment works best for large flat surfaces, and when you need to treat a long series of similar objects. Your spraying method will depend on which type of paint you’re using and on the form and material of the object. Different spraying techniques include conventional, Airless, Air-assisted, and electrostatic spraying. Two-component airless spray equipment is becoming more common for the application of water-borne epoxy and polyurethane paints, especially when applying large volumes of paint.
Ensure proper metal paint drying conditions
Some water-borne metal coatings can be applied in a single thicker layer, but most require two or three more layers. In these cases, you need to include proper drying time in between each layer. The recommended temperature for drying depends on the specific paint. Proper ventilation is also crucial with water-borne metal coatings.
When it comes to drying, water-borne products are more sensitive to the climate. The temperature of the ambient air, surface, and paint should not fall below 15°C during application and drying. The recommended humidity level for water-borne paints is 20-70%. For the best results, you need to apply the paint in an environment where you can control the climate. If the environment is too humid, water from the paint can’t evaporate properly and is more prone to sagging. On the other hand, too low humidity may cause problems with the film forming properties, increasing the risk of dry spray.
Maintain your water-borne metal coatings
Some people may worry that water-borne coatings require extra maintenance, but this is not the case. Besides in extreme conditions, these products require the same maintenance period as other alternatives, meaning some minor maintenance will likely be needed along the way.
The equipment you use for maintenance might not be the same as what you use for application. For off-site maintenance and touch-ups, you might use brush and roller application methods. Brushes made of synthetic material such as polyamide (nylon) or polyester, with bristles with thinned or split ends, are specially suitable for water-borne paints.
Following these expert tips will help you ensure the best results with your water-borne metal coatings—all while having a more positive effect on the environment and improving users’ health and safety.
Want more insights and advice about working with water-borne metal coatings? Subscribe to our newsletter, and get in touch with us if you have any questions!