Different types of industrial metal coatings
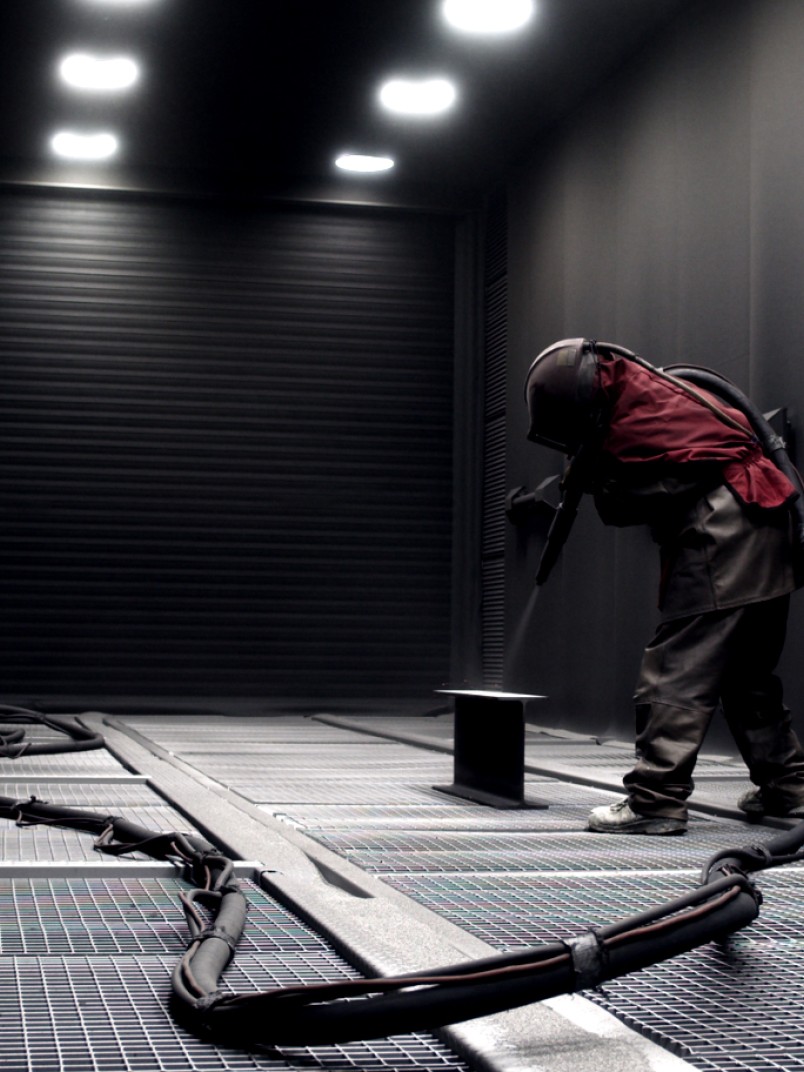
Tikkurila offers a wide range of painting systems for metal surfaces that meet the highest quality standards. Our wide selection of metal coating products includes different kinds of metal coating products from traditional alkyd paints to modern high-tech DTM polyurethanes including solvent-borne primers and topcoats, more environmentally sound high-solids paints, solvent-free coatings, and water-borne products.
The main purpose of all the metal coatings is usually the same, to protect against corrosion, but there are different kinds of products that can be divided into product groups in several different ways. If you want to learn more about the purposes of metal coatings and their use and how to pick the right coating for your needs, please read more here.
Industrial metal paints usually consists of resin, pigments, solvents and additives. Generally, paints are classified depending on their resin, or in which way the paint cures. The resin has the most important influence on the properties of the paint.
How to categorise different kind of industrial metal paints based on how the resin dries
Paints can be divided into physically drying and chemically drying paints, depending on the way their resin hardens. Paints are also often divided into water-borne and solvent-borne paints.
Physically drying paints
The paint film of physically drying paints is formed when the solvents evaporate and the molecules of the resin coalesce to form a film. The drying rate is based on how fast the solvents evaporate and the thickness of the coating.
These types of coatings will dissolve in their original solvents and soften at higher temperatures. Similarly, water-borne paints dry physically when the water and trace solvents evaporate. However, water-borne coatings do not dissolve in water after they have dried. Physically drying paints include acrylic, vinyl and chlorinated rubber paints.
Chemically drying paints
The paint film of chemically curing paints is formed in a chemical reaction where the liquid resin, consisting of small molecules, cures to form larger molecules. If the paint contains solvents or water, the drying begins with the evaporation of these volatile components.
The cured film is not thermoplastic. Neither does the film dissolve in solvents, but if the grade of curing is low, the coating may expand under the influence of solvents.
Chemically curing paints can also be divided as below:
- Paints which dry by oxidation cure by reaction with oxygen in the air (e.g. alkyd paints)
- Paints which are moisture curing dry by reaction with humidity in the air (e.g. moisture cured urethanes and ethyl silicate paints).
- Two component paints, where the components react with each other (e.g. epoxy and polyurethane paints)
- Stoving enamels, where the components react with each other under the influence of high temperature.
Water-borne paints
In combination with many other recent technical improvements, water-borne protective paints can be used for steel surfaces without compromising anti-corrosive protection or other properties. Water-borne paints use the same types of resins as solvent-borne paints. Tikkurila offers a good selection of water-borne options for acrylic, polyurethane, epoxy, alkyd and intumescent paints.
The properties of water-borne paints are developed to be similar to corresponding solvent-borne products. Beside the environmental benefits, there are several advantages in using water-borne coatings.
Water-borne coatings reduce fire and explosion risk and improve the working environment. Water can be used as thinner and cleaner instead of solvents. There are also some disadvantages when using waterborne materials. They are sensitive to impurities of the substrate being coated, so that cleaning has to be to a very high standard. Blast cleaning to Sa 2½ is the normal standard required for good performance. See Tikkurila's selection of industrial water-borne coatings for metal.
Alkyd paints
Alkyd paints generally have good resistance to weathering and abrasion. They are one component, easy to spray and the relatively low in price. They often have good resistance to heat, and to splashes of oil, water and fuel, but they tend to have limited resistance to acids and alkalis. Alkyd paints can be used indoors in modest gas and chemical dust exposure, and outdoors in urban, industrial and marine environments.
Alkyds are polyesters which contain fatty acids derived from vegetable oils. Alkyd paints dry, when solvents evaporate and resin reacts with the oxygen in the air. Drying by oxidation needs time and alkyd paints usually reach their protective properties within two weeks. Drying oils are used in air-drying paints. Non-drying oils are used in stoving enamels. The solvents in alkyd paints are mostly white spirit or xylene.
If the recoating has been done too soon it can cause wrinkling, or “lifting” (detachment of the initial coat from the substrate). Grinding or too strong solvents in the topcoat may also cause lifting of alkyd paints. In the data sheets for alkyd paints the recoating times and suitable topcoats are recommended.
The properties of alkyd paints can be improved by adding vinyl, phenolic or acrylic resins. Epoxy esters and urethane alkyds are also resins, that dry by oxidation and their properties are similar to alkyds. Their abrasion and chemical resistance is slightly better than alkyds. Epoxy esters are generally used only in primers.
Acrylic paints
Acrylic paints are one-component physically drying primers and topcoats. There are also products that are developed to be used as a single coat paint system for steel structures in interior and exterior structures.Typical uses are e.g. steel frameworks, machinery and equipment.
Waterborne acrylics are environment friendly easy to use options for protection of steel surfaces. There are also options for shop primers and dipping application. Acrylics can provide excellent adhesion to many substrates. They are fast drying and therefore optimal for fast production lines.
Epoxy paints
Epoxy paints are 2-component paints that are commonly used for metal and concrete surfaces exposed to mechanical and chemical stress even in most demanding environments and can be modified for different purposes. They can also be used in many different ways. (single coat, filler, primer, intermediate or topcoat).
Epoxy coating cures as a result of chemical reaction of two components mixed. Solid epoxy resins are generally used in solvent-borne paints and liquid epoxy resins in solvent-free coatings.
Epoxy paints forms a film that does not dissolve in the original solvents and has good heat resistance. Chemical and mechanical resistance of epoxy paints are good. Coatings are hard and elastic and have good adhesion to metal surfaces. Properties of the paint can be adjusted by the choice of the hardener and the type of epoxy resin.
When exposed to UV-light (sunlight), epoxy coatings will “chalk”, meaning they matt down and loose colour. Even so, they are often specified for exterior use in aggressive chemical environments. The colour should be chosen to minimise the effect of chalking If the surface is not top coated with for example polyurethane paint.
Usually epoxy paints require at least a temperature of +10°C for curing. New, low temperature curing, so called WG (winter grade) epoxies cure down to temperatures of -5°C. In normal temperatures the WG products cure faster than ordinary epoxy paints. This reduces the recoating interval, which is an advantage in paint shops.
Learn more about Tikkurila's epoxy paint Temacoat HS-F Primer.
Polyurethane paints
Polyurethanes are generally used as topcoats for paint systems in all kinds of exterior environments. There are also many options with anti-corrosive pigments for single coat, direct-to-metal use.
Polyurethanes are flexible, gives an easy-to-clean finish with good gloss and colour retention. They do not chalk like epoxies. Because of their UV resistance they are often used as topcoats over epoxy build systems for external surfaces like cisterns, steel masts, transport equipment, machines etc.
Base in two component polyurethane paints consists generally of polyester, acrylic, polyether or epoxy resins containing reactive hydroxy groups. Hardener consists of aromatic or aliphatic isocyanate which forms the polyurethane when reacting with the base.
The properties of the paint can be adjusted by choice of the components. By using an aliphatic hardener, a weatherproof and non yellowing paint can be produced. Aromatic hardeners are used only for indoor use.
Learn more about Tikkurila's polyurethane paint Temathane PC 50.
Oxirane ester paints
Oxirane ester paints are often used instead of epoxy and polyurethane paints as a more environmentally friendly and labour-safe alternative.
Oxirane ester paints are two-component paints, which consist of modified oils and polyester, with high acid content. The film is formed when the oxirane and the carbonyl groups in the resins react with each other. The drying and elasticity properties of the paints can be adjusted within a certain range by changing the relation between the resins.
Oxirane ester paints are resistant to a wide range of chemicals, except alkalis. They are resistant to grease, oil and splashes of solvents. They are also resistant to non oxidising acids and salt solutions. They have good resistance to sulphuric acid and to water immersion. They also have good colour and gloss retention.
Chlorinated rubber paints
Chlorinated rubber paint systems are recommended for steel and cast iron surfaces exposed to moderate chemical stress, e.g. bridges, cranes, haulage equipment, harbour equipment and outside surfaces of cisterns. The main resin of the paint is chlorine paraffin softened chlorinated rubber and the solvents are generally aromatic hydrocarbons. They are fast drying and it is also possible to apply them in cold conditions, down to -10°C.. The coatings withstand +80°C dry heat, but are not usually recommended for temperatures above +60°C.
Chlorinated rubber topcoats are also suitable as vapour barrier coatings on concrete surfaces.
Zinc-rich paints
Zinc-rich paints are commonly used in systems for most demanding environments like bridges and offshore or coastal structures. A zinc dust paint film gives cathodic protection to the steel. Paints can be called zinc-rich when the zinc dust exceeds 80% of the solids by weight. Various standards give different levels for the amount of zinc required for a ’zinc-rich’ coating, with levels varying between 75 and 90 percent by weight.
The difference compared with galvanizing is the resin in the paint. The resins in zinc dust paints are usually epoxy, alkyl silicate or some physically drying resin. The choice of resin for zinc dust paints is important because properties such as hardness, elasticity, adhesion to the substrate and overcoating depend mainly on the resin.
Zinc silicate paints are two-component paints based on solvent-borne ethyl or water-borne alkali silicate resins. Ethyl silicate paints are the most common. Ethyl silicate paints cure by reaction with atmospheric moisture. Therefore the relative humidity of the air has to be relatively high (~80%) in order to ensure curing. Ethyl silicate paints can also be applied at low temperatures. They are used for solvent resistant coatings and as primers for long term exterior exposure systems.
Silicone paints
Silicone paints are used as weatherproof topcoats and, when pigmented with aluminum, for painting of hot surfaces. Pure silicone paints withstand +650°C dry heat on their own, and when applied over zinc silicate primers, up to +400°C. Silicone paints are used indoors and outdoors for hot surfaces.
Intumescent paints
Intumescent paints are used to protect the substrate from the effects of fire. Intumescent painting of structural steel retards the heating of the steel and gives additional time before the steel reaches a temperature at which it looses load bearing capacity. This extra time allows evacuation of the building and a chance for the emergency services to control the fire.
Most single pack Intumescent paints are only used in dry interior areas. A typical system would be: blast clean to Sa 2½, approved anticorrosive primer to around 75 microns, the Intumescent coating, and usually a topcoat to around 40 microns dft. The dry film thickness (generally 0.5-3.0mm) of the Intumescent paint is determined by the size and weight of the steelwork and the period of fire protection required.
Read more about our solutions for intumescent coatings.