Metal Coatings: The complete guide for industrial applications
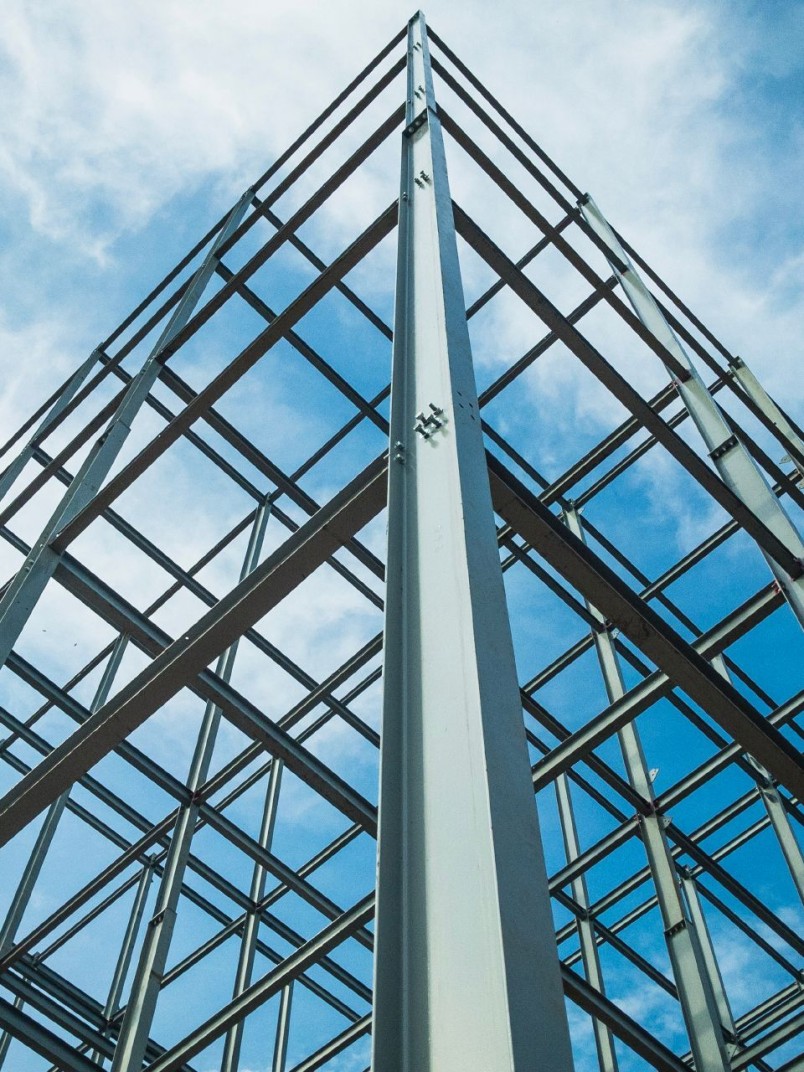
Table of contents
What are metal coatings?
Metal coatings refer to paint that is applied to metal to protect surfaces and prevent corrosion in order to increase the product’s lifespan.
In short: Every paint is a type of coating, but every coating is not a paint. Coating can consist of many layers of paint and refers to the end result that remains once the work is finished.
There are multiple types of metal coatings, including simpler metal coatings and metal surface treatments, as well as more corrosion-resistant metal coatings.
To fully get a grasp on the different types of coatings, let’s go a bit deeper into the chemical components that make up industrial paints for metal. The most important component is the resin; and that could be epoxy, alkyd, acrylic, polyurethane, and more.
Next is the solvent, which is what essentially transforms the paint into a liquid. In the process, all the pigments and other raw materials are dispersed or mixed in water to form an even liquid. This component can be a chemical solvent or water. Due to this, coatings can be categorized as either solvent-borne or water-borne depending on the solvent used. Other components that are used in a paint formula are pigments, fillers, thickeners, and other additives.
At Tikkurila, our product range for metal surfaces varies from traditional alkyd paints to modern high-tech direct-to-metal (DTM) polyurethanes. These include solvent-borne primers and topcoats, more environmentally sound high-solids paints, solvent-free coatings and sophisticated water-borne products
What are the purposes of metal coatings?
Rymas Herman, General Industrial Regional Director North & East, discusses the main purposes of metal coatings.
What are the purposes of metal coatings?
Different types of metal coatings are naturally recommended for different types of purposes and industries. Let’s go through some of the most common purposes for metal coatings.
Corrosion protection
The main purpose of all types of metal coatings is simply to protect metal products from natural occurrences such as corrosion. Both water-borne and solvent-borne coatings work well in industrial use, but different types of coatings have different pros and cons. This means that before deciding on which coating to go with, you should always consider specific products and the specific use case at hand.
There are many different metal coating methods for corrosion prevention, and due to their various features and qualities, each type performs differently and according to different parameters.
Better durability
In addition to protection from corrosion and natural elements, using quality metal coatings ensures better durability for the entire metal structure.
Coatings that last longer also directly result in longer maintenance painting intervals, which in turn helps you manage costs in the long run.
Improved appearance
Metal coatings result in the long-term preservation of a structure’s cosmetic appearance, even under extreme conditions. With suitable and proper metal coatings, you can create a long-lasting finished surface with your preferred aesthetics including paint colour, gloss level, and more.
Increased chemical and water resistance
Applying a proper metal coating means forming a tough surface on your structure, and, in addition to protection from corrosion, the coatings are also highly resistant to any abrasion or chemical stress.
If you need a metal coating for an environment of high humidity, it’s a good idea to consider solvent-borne coatings. To find out more about their differences and which ones you should consider for your structure, you can read our article on the differences of water-borne and solvent-borne coatings.
Fire protection
Certain metal coatings can also be used to protect the substrate from the effects of fire. Having a metal coating that protects from fire helps by giving additional time before the steel reaches a temperature at which it loses its load bearing capacity. This extra time allows evacuation of the building and a chance for the emergency services to control the fire.
For example, one of our products — the Fontefire ST 60-1 — is a water-borne one-component intumescent coating that provides you with a heat expansion binding reaction that results in the creation of an insulating foam layer, which then protects your metal structure from reaching critical temperature for a certain period of time.
How are metal coatings used?
Our wide range of different painting systems for metal can be used for any metal surface, whether interior or exterior, and we offer ready-made solutions for selected industrial segments.
All of our different coating and surface treatment systems for metals have different use cases. For instance, maybe you need metal coatings for a harbour environment, where your structures are frequently subjected to harsh working conditions and corrosive climate stress. In these types of conditions, machinery and equipment require a higher level of protection than the same machinery used indoors.
Painting of Mitsubishi Logisnext truck masts
We react to our customers' challenges with prompt but careful product development. When Mitsubishi Logisnext needed a solution to achieve environmentally sustainable emissions targets, Tikkurila Temasolid SC-F 20 was developed for painting truck masts of Mitsubishi Logisnext.
Tikkurila Temasolid SC-F 20 helps to reduce emissions from the painting process. It contains less solvents than the product used before and dries faster than before, at an even lower temperature. As environmental and efficiency targets become more stringent, industry requires increasingly low-solvent products.
The benefits of customised product development will eventually be used by the entire industry.
As another example, you might need high-performance, environmentally compliant solutions for the agricultural, construction, and earth-moving machinery and equipment (ACE) market. Our high-performance systems include water- and solvent-borne solutions that provide better protection while using fewer coats of paint.
Our solutions for different types of steel structures include coatings that protect against mild stress for interior surfaces, heavy stress for exterior surfaces, or even extreme chemical stress. We also offer a wide color range, including metallic colors that can also provide an aesthetic dimension.
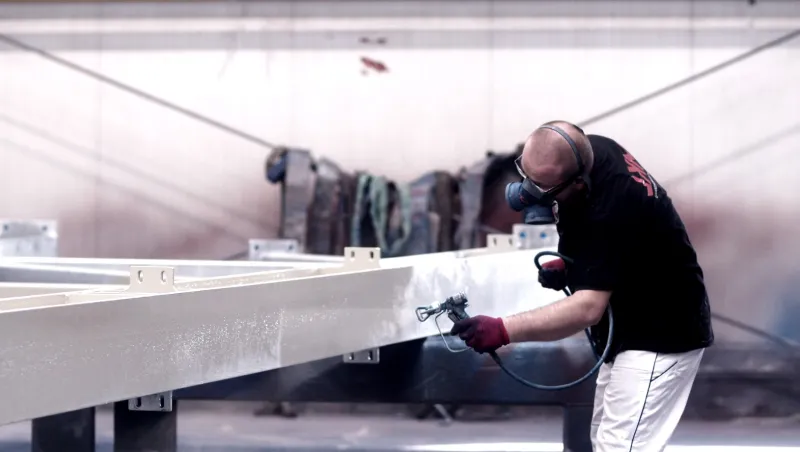
Polish construction professional MKL BAU
Polish construction professional MKL BAU chose Tikkurila's coating solutions because Tikkurila products suit perfectly their projects’ needs. Marius Cizio, the member of the board and co-owner in MKL BAU has been very satisfied with Tikkurila.
“Tikkurila products guarantee excellent durability for our steel structures. And our clients trust Tikkurila and its products.” says Cizio.
MKL BAU sp z o.o. offers design, material delivery and erection services for business sectors such as energy, civil and industrial construction. They specialize in design, production and engineering.
Watch the video and learn more about why MKL BAU chose Tikkurila coating solutions.
There are many paint systems for maintenance and touch-up painting that are easy to use and do not need blast cleaning surface preparation. We also offer a system for surfaces immersed in water.
If you are not sure what kind of painting system or coating and surface treatment system you need for your specific metal structure, please feel free to contact us to find out more about your options.
Different types of coatings for metal
As mentioned above, different types of metal coating products range from traditional alkyd paints to modern high-tech DTM polyurethanes including solvent-borne primers and topcoats, more environmentally sound high-solids paints, solvent-free coatings, and also sophisticated water-borne products.
Next, let’s do an overview of the different categories of metal coatings.
Picking the right types of metal coatings
As there are many different types of metal coatings, there are naturally multiple different factors to consider when choosing the right coating product for your specific needs.
Your goals
To make the right choice, take the time to consider your goals with metal coatings. Ask yourself the following questions before making a decision:
- What kind of painting conditions are we working with?
- What kind of environment is our end product used in? (Is it indoors? Or are there harsh weather conditions?)
- How long do we want the paint to hold? With some products, such as mining equipment, the paint is not expected to stay on the surface for longer than for the product’s first use.
- What is our company’s mindset towards sustainability? You might choose to use water-borne coatings, for example, if your company’s long-term goal is to reduce your VOC emissions and the negative impact your operations have on the environment.
- What demands are we currently facing?
- Which painting system standards do we have to comply with?
Your processes
Consider the following questions about your current ways of working:
- What paints and coatings for metal surfaces are we using today?
- What types of metal surfaces are we working with?
- What equipment are we currently using?
- Do we paint first and then assemble, or is it or other way around?
The project timeline and deadline
Ask yourself the following questions when considering your project timeline:
- What drying time do we need?
- When are we able to pack the dried product?
- How much should we be able to paint in one day?
Your budget and costs
Finally, consider your budget. Remember that some products require a higher initial investment but pay off in the long term. For example, water-borne products are priced a bit higher because the raw materials to develop these products are priced higher. But after the initial investment of adjusting our equipment and processes, you start gaining back your investment. In fact, you can reduce your overall operations cost by using water-borne products. You don’t need to invest in explosion-proof equipment, highly flammable paint insurance, or specially trained personnel to transport the products because water-borne products aren’t flammable. Plus, wet water-borne paint can be cleaned with water, meaning you’ll save expenses by not using as many cleaning supplies.
Additionally, using DTM products rather than primers and topcoats will help reduce process time since only one application is needed.
Remember that the cost of paint is just one part of the total project cost. The true cost of painting an object or unit takes into account all aspects of the treatment. And depending on what paint products you use, the total cost can be reduced by less dry film thickness (DFT), and shorter process time (application, drying).
Use our cost calculator for metal products to better plan your budget.
Metal coating standards - What you should know?
As with any field or industry, there are certain standards and regulations that need to be taken into account when deciding which product to go with.
With metal coatings, all the materials and systems you use need to fulfill either international standards like ISO 12944, which is a global corrosion protection standard, or any internal standards your individual customer may have.
This means, in short, that all systems need to be properly tested to these standards.
The materials and systems we at Tikkurila supply comply with ISO 12944. Part 5 of this standard defines protective coating systems for different corrosive environments: C2, C3, C4, C5. The standard also determines durability ranges, which affects the time to the first major maintenance round: L, M, H and VH.
Tikkurila also has paint systems approved according to other standards as well. These include Norsok (Norway), Silko (Finland), GOST (Russia), and so forth.
Part 5 of ISO 12944 defines protective coating systems for different corrosive environments: C2, C3, C4, and C5, and it also defines systems according to their ISO 12944 corrosion class.
The standard also determines durability ranges, which affects the time to the first major maintenance round: L, M, H, and VH.
Working with metal coatings
Žydrūnas Čepkauskas, Strategic Business Development Manager, shares expert tips for working with metal coatings.
Next, let’s go through a couple of useful expert tips for working with metal coatings—from surface preparation to maintenance.
Metal coating equipment
For different types of coatings, different equipment is required in order to allow the product to work its magic.
For example, solvent-borne metal coatings require special explosion-proof equipment, as the products are highly flammable. In turn, water-borne products aren’t flammable and don’t require such equipment. On the other hand, water-borne products still require equipment with stainless steel in all parts that are in contact with the wet water-borne paint.
Surface preparation
The success of your metal surface treatment largely depends on the surface to which it’s applied. Before applying the coating on your metal surface, the surface needs to be properly cleaned and roughened to ensure adhesion. The right level of cleanliness will help ensure the right performance of the coating.
For instance, solvent-borne coatings are more forgiving of contaminated surfaces, while water-borne coatings always require a clean environment and surface—so, depending on which type of coating you are going with, ensure that the level of cleanliness is up to par with what the product requires.
You can follow this example of a water-borne product’s recommended surface cleaning:
- Steel surfaces: Degrease and blast clean to grade Sa2½. (ISO 8501-1) If blast cleaning is not possible, phosphating is recommended for cold rolled steel to improve adhesion.
- Primed surfaces: Oil, grease, salt, and dirt are removed from the surface by appropriate means. Repair any damage to the primer coat. Check your product's PDS for guidance regarding previously primed surfaces.
Application
Your application methods could depend on several factors such as your equipment, the type of paint you’re using, production speed, output speed, and whether you’re applying on-site (at the painting shop) or off-site.
Depending on these factors, you might use application robots, automatic painting lines, and different spraying techniques such as conventional, Airless, Airspray, and electrostatic spraying. For off-site maintenance and touch-ups, you might also use brush and roller application. No matter which method you use, correct paint application is key to get a long-lasting finish with metal coatings.
Drying
If you are painting in very humid conditions, you might need to pay extra attention to drying.
Especially with water-borne coatings, the water in the paint can’t evaporate properly in extremely humid conditions, and thus the paint will take longer to dry.
A possible solution for this is to apply metal coatings in a room where you can control the climate and keep the humidity at a certain percentage. The recommended humidity level is 20-70%.
In many cases you may fasten the drying time by increasing the temperature. The recommended temperatures depend on the paint.
Maintenance
The correct surface preparation and paint application will improve the coating’s performance lifetime, but some maintenance will most likely be needed after a period of time when working with metal coatings.
There’s a wide selection of repair and maintenance products for industrial metal surfaces to choose from, and we at Tikkurila are of course available to answer any questions you may have.
Chemical resistance
You might need metal coatings that require specific chemical resistance, such as oils, fuels, acids, and chemical solvents, among others. When considering metal coatings for a particular chemical environment, consider the following factors:
- Chemical exposure
- Operating temperature
- Mechanical abrasion
- Degree of protection required (immersion or splash/continuous or limited)
Conclusion
To sum up everything we’ve gone through, there are multiple types of metal coatings, including simpler metal coatings and metal surface treatments, as well as high-tech protective metal coatings—all of which are designed for different purposes.
If you are interested in finding out more about all things coating-related, subscribe to our newsletter here. We share timely and relevant information and updates, and never bother you unless we have something interesting to say.
Just fill in the form below and we'll send a copy to your inbox!