The truth behind 6 common water-borne metal coatings misconceptions
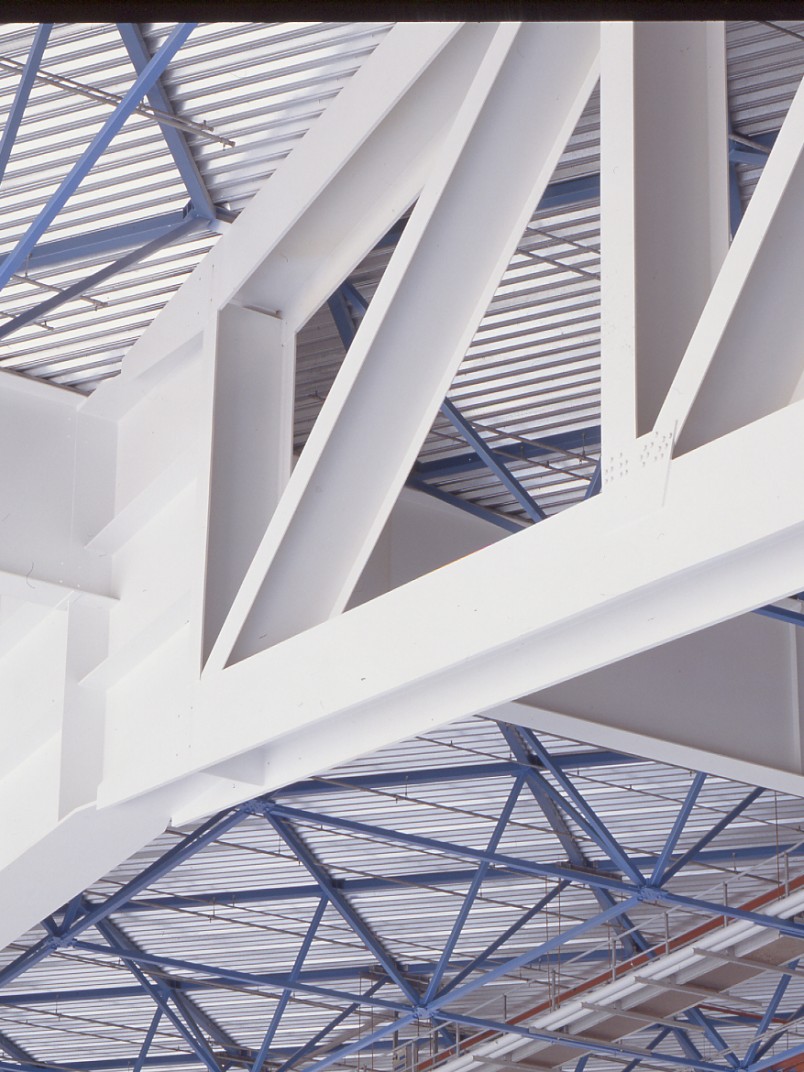
Water-borne solutions haven’t been around as long as solvent-borne solutions. And while they’re rising in popularity, water-borne industrial metal coatings are not as widely used across the globe. There are many misconceptions about water-borne solutions—but these are based on rumours rather than facts. Before choosing metal coating products, it’s crucial to know as much information as possible about them. To help you get the information you need, we broke down six common misconceptions about water-borne coatings for metal surfaces.
1. Water-borne products do protect against corrosion
One of the main misconceptions about water-borne coatings is that they can’t protect metal surfaces from corrosion. When considering anti-corrosion properties, it’s important to note that the liquefying agent in paint—whether a chemical solvent or water—is only carrying the paint film that forms corrosion-inhibiting materials to the substrate. The water in water-borne products then evaporates from the film, just as chemical solvents do. Whether the coatings are solvent-borne or water-borne actually has no effect on the corrosion later.
Since rust requires water to form, many people worry that water-borne coatings aren’t anti-corrosive. In reality, water-borne coatings do protect against corrosion—it’s one of the product’s main purposes.
Additionally, some people might worry about flash rust, which is rust that forms when the paint is still wet because of the water in water-borne products. Flash rust can occur if the user is applying the product incorrectly, or because of the paint formulation. Flash rust, however, does not always occur with water-borne coatings. At Tikkurila, for example, we formulate our water-borne products to avoid flash rust.
2. Water-borne products do offer good weatherability
Weatherability is another top concern among those comparing different types of coatings for metal. You might be wondering: Are water-borne coatings resistant to UV light and weather conditions?
Water-borne products have the same weatherability as solvent-borne alternatives, and sometimes even better weatherability. However, the anti-corrosive and weatherability properties will depend on the chemistry of individual products. Instead of comparing water-borne coatings to solvent-borne coatings for weatherability, you’ll need to compare specific products, including epoxy, acrylic, and polyurethane. For example, acrylics are highly durable water-borne metal coatings that offer good corrosion protection.
It’s important to note that water-borne coatings aren’t used for immersed services or for buried and underground services. The weather resistance required for marine coatings isn’t yet possible with water-borne products. Water-borne coatings are also more sensitive to the climate when it comes to application and drying, so controlling the environment’s humidity is key.
3. Water-borne metal coatings perform as well as solvent-borne coatings
Another common misconception is that water-borne coatings are inferior to solvent-borne coatings when it comes to performance. It’s fair to question the quality of water-borne products as your metal coatings should perform at the level you need them to. But water-borne coatings don’t perform any worse than solvent-borne alternatives—they protect metal surfaces and offer high-quality end results.
There have been many advancements with the chemicals and resins in water-borne products—they are continually being improved to meet industrial performance standards. While solvent-borne coatings have traditionally been used for metal surfaces, these new advances and additives to paint formulations allow water-borne products to improve in performance.
When applied correctly, water-borne coatings result in a smooth, long-lasting finish. They will even perform well and protect metal surfaces in harsh environments. The Tikkurila water-borne Fonte range, for example, compares favourably with solvent-borne coatings. As an example, the Fontecoat EP 80, a two-component water-borne epoxy topcoat, forms a tough and glossy surface that is highly resistant to abrasion and chemical stress.
4. No extra maintenance is needed when working with water-borne solutions
Besides in extreme conditions, water-borne solutions require the same maintenance period as other alternatives. Just like solvent-borne coatings, water-borne coatings are properly researched and tested to ensure quality and durability. A little maintenance will most likely be needed along the way, but correct surface preparation and paint application will improve the coating’s performance lifetime.
As with solvent-borne products, you can choose from a wide selection of repair and maintenance products for industrial metal surfaces.
5. Switching to water-borne solutions offers a return on investment
While switching to water-borne solutions generates an initial cost, once all of the equipment and processes are adjusted, you start gaining back your investment. The main reason why water-borne products are priced a bit higher is because the raw materials to develop these products are priced higher. But using water-borne products can actually reduce your overall operations costs. Since water-borne products aren’t flammable, they don’t require explosion-proof equipment, highly flammable paint insurance, or specially trained personnel to transport the products. And since wet water-borne paint can be cleaned with water, you won’t need to use as many cleaning supplies.
When using water-borne solutions for the first time, they might be a bit more challenging to work with compared to solvent-borne solutions. For example, when applying water-borne products, you need to make sure the environment and metal surfaces are clean. To ensure good results, you need to be a bit more precise and accurate in the application process. You may need to apply two or three layers of paint due to the low solid content of water-borne products.
At Tikkurila, however, we support our customers to ensure a smooth transition to water-borne solutions. We test water-borne products together with our customers, see how it works, and discuss solutions for any problems that arise.
6. Using water-borne solutions could improve your business
Depending on the situation in your country or company, you might be wondering if using water-borne solutions will help you grow your business. Should you make the switch? Depending on your goals and situation, water-borne products aren’t always the right choice. But it’s important to be aware of the growing demand for water-borne products, and the ways they can improve your business. In fact, the global water-borne coatings market size is expected to progress at a CAGR of 5.7% from 2017 to 2025.
One of the main reasons companies choose water-borne solutions is to lower their negative impact on the environment. Unlike solvent-borne coatings, which emit high levels of volatile organic compounds (VOCs), water-borne products emit low or no VOCs. When water-borne paint dries, water rather than toxic chemicals evaporate into the air. With rising sustainability concerns, and stricter VOC and safety regulations coming, water-borne solutions are gaining in popularity.
Water-borne solutions also result in safer working conditions. Improving users’ health and safety and reducing explosion risk are also among the top reasons companies choose water-borne solutions.
- Questions to ask yourself when considering water-borne solutions
- What paints and coatings for metal surfaces are we using today?
- What types of metal surfaces are we working with?
- What equipment are we currently using?
- What is our company’s mindset towards sustainability?
- What are we aiming for with metal coatings?
- What demands are we currently facing?