Water-borne vs. solvent-borne metal coatings: A comparison for industrial applications
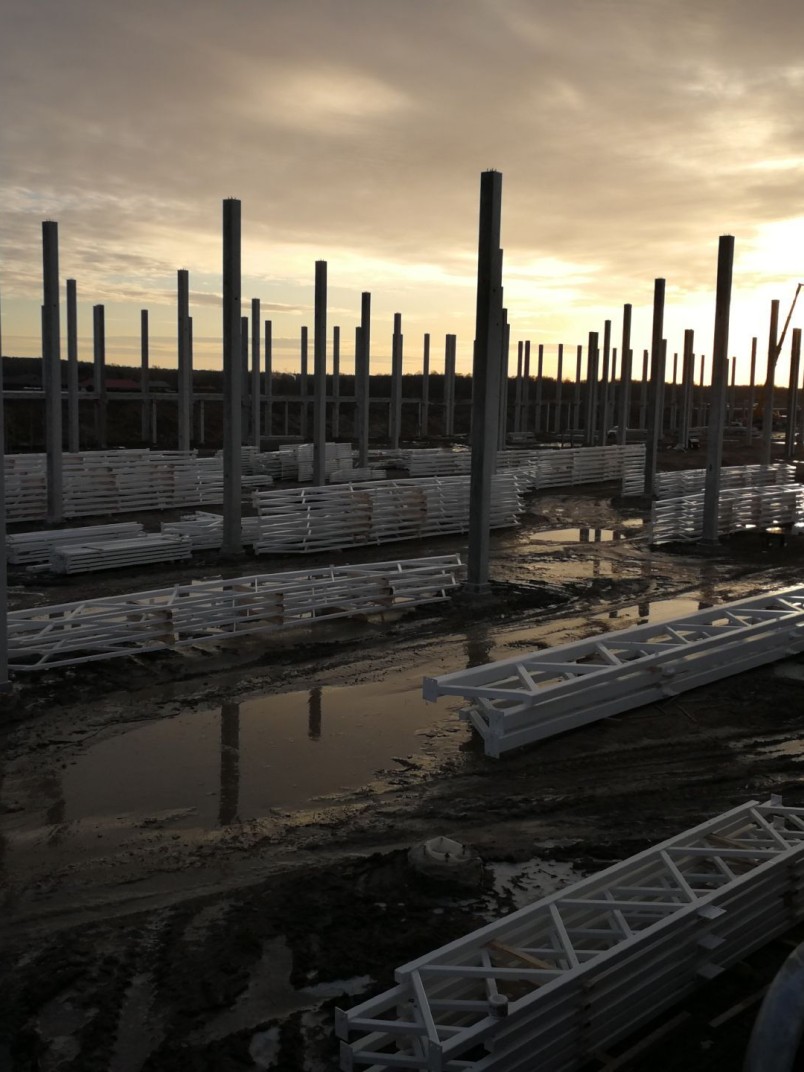
What do water-borne and solvent-borne coatings have in common, and what are the main differences between these two types of products?
First, let’s consider the chemical components that make up metal coatings: The most important component that determines the properties of the coating is the resin, which could be epoxy, alkyd, acrylic, or polyurethane. Another main component is the solvent, which is what disperses the paint into a liquid. This component can be a chemical solvent or water. As the coating is applied and it dries, the solvent is evaporated from the coating and what is left in the coating is everything else that was in the formula. Other components in a paint formula are pigments, fillers, thickeners, and other additives. Coatings are then categorized as solvent-borne, or water-borne depending on the solvent. While almost all coatings were solvent-borne years ago, advancements in paint and coating technology have led to the development of water-borne products.
The purpose of water-borne and solvent-borne metal coatings is the same: to protect metal products from corrosion. But the features and properties of the binders in solvent-based coatings are different than in water-based coatings. As a result, each one performs differently according to different parameters.
Both solutions have their own advantages, so how can you choose the right products for your company? To make better informed decisions, find out exactly how water-borne coatings differ from solvent-borne coatings.
Volatile organic compounds (VOCs)
The most harmful environmental effect of solvent-borne paints and coatings is the evaporation of solvents—VOC emissions—which increase ground-level ozone formations and enhance air pollution. Strict environmental legislations have required companies to reduce the levels of VOCs they emit. And more countries will be creating legislations that prohibit the use of solvent-borne solutions due to their high VOC emissions.
On the other hand, almost only water evaporates from water-borne products. Especially in the application phase, the environmental impact of water-borne products is much smaller than that of solvent-borne products. And since you can clean wet water-borne paint with water, there are no extra VOC emissions from the cleaning process.
The rising importance of sustainability has been the key reason why more and more companies use water-borne solutions. Companies can reduce their VOCs by using water-borne coatings, having a positive impact on the environment and meeting stricter environmental standards. Taking concrete steps to improve sustainability can also improve your brand image.
Health & safety
The fumes from solvent-borne products smell strongly and are dangerous for humans to inhale. While getting water-borne coatings on human skin is not good, it’s not as harmful as being exposed to solvent-borne paint. Water-borne solutions are a safer choice for both the environment and the health of the individuals handling the products.
It’s important to note that no matter what product you’re working with, users always need to properly protect themselves—during spraying, inhaling water-borne related compounds are as hazardous as solvent-based compounds. It’s during the drying process that the water, instead of organic solvents, are evaporating, meaning that inhalation is not as hazardous. Overall, using water-borne coatings means less risk, irritation, and other harmful effects for the user.
Shelf life
Solvent-borne products have a shelf life of approximately two years, while most water-borne products have a one-year shelf life. The reason for this is that bacteria lives in water. However, it is possible to extend the shelf life of water-borne products by adding specific chemicals (eg. biocides) to the formulas but it is good to remember that too much biocides can be harmful to the environment and health which is why they must be used safely and sustainably.
Anti-corrosive & weatherability properties
The raw materials in water-borne coatings are different than in solvent-borne coatings since they need to be stored in water. But the thinner—whether a chemical solvent or water—is only carrying the important paint film forming and corrosion-inhibiting materials to the substrate. They evaporate from the film and are thus not there to affect the corrosion later.
People unfamiliar with paints and coatings may think that since water causes metal to rust, water-borne products cannot be anti-corrosive. Some water-borne product users become especially concerned about the coating quality when they see flash rust. Flash rust is rust that forms rapidly when the paint is still wet because of the water in the paint product. But this is something that can be prevented. At Tikkurila, for example, we formulate paints so that flash rust does not form.
When considering the anti-corrosive and weatherability properties of metal coating solutions, you need to consider specific water-borne and solvent-borne products. Comparing polyurethane to epoxy would be like comparing apples to oranges. Water-borne acrylic products, for example, could offer better weatherabilty than some solvent-borne products, especially when it comes to colour and gloss stability.
Application conditions
Solvent-borne products are a bit easier to work with because they are more forgiving of contaminated surfaces. For example, you can still use solvent-based coatings when there are traces of grease and dirt on the metal surface they’re being applied to. With water-borne solutions, a clean environment and surface is necessary. You need to be more precise, accurate, and clean throughout the process to ensure good results.
Additionally, you can use a bit less of the product with solvent-borne coatings and still have good protection. With many solvent-borne products, you can apply a single layer directly to a rough metal surface and get good coverage, a nice layer, and an even surface. Solvent-based coatings take out the structure of the substrate, meaning no scratches or tarnishes will be visible. The solid content in water-borne products are generally lower than in solvent-borne products. As a result, more water-borne paint needs to be applied to have the same dry film. Some water-borne paint can’t be applied in a single thicker later—you need two or three more layers with drying time in between each layer. There are also some products, however, that can be applied in just one layer.
NORSOK M-501 System 1 | ||||
---|---|---|---|---|
Product type | Water-borne system | µm DFT | Solvent-borne system | µm DFT |
Zinc rich primer | Temazinc 99* | 60 | Temazinc 99 | 60 |
Epoxy intermediate | Fontecoat EP 50 | 160 | Temacoat Primer | 160 |
Polyurethane topcoat | Fontedur HB 80 | 60 | Temathane PC 80 | 60 |
* solvent-borne |
The water-borne Fontecoat EP 50 160 µm, as seen in the table above, is what is required to meet the specification and the quality level. However, it’s important to note that EP 50 must be applied 2 x 80 µm to get 160 in the end. With the solvent-borne counterpart Temacoat Primer, you can apply a single layer 160 µm.
When it comes to application and drying, water-borne coatings are more sensitive to the climate. They aren’t generally used for immersed services (underwater) or for buried and underground services. If the climate where you paint has high humidity, the water in the paint can’t evaporate properly, and the paint will take longer to dry. In winter months, for example, you might have some trouble with dry spray and bad flow and levelling. In summer months, you might experience some issues with drying and sagging, which could also happen with solvent-based coatings.
The solution is to apply metal coatings in a room where you can control the climate and keep the humidity at a certain percentage—the recommended humidity level is 20-70%. Doing so will be advantageous in both winter and summer since the extremes are levelled out.
Metal coatings equipment, cleaning, and disposal
One of the main differences between solvent-borne and water-borne coatings is that solvent-borne products are highly flammable. Because of this, transportation, storage, and disposal of solvent-borne products needs to be done by specially educated personnel. According to the European Agreement concerning the International Carriage of Dangerous Goods by Road (ADR), these products can’t just be shipped in any truck. Plus, they require special explosion-proof equipment. The insurance for such flammable paint can also be higher in some countries.
Water-borne solutions aren’t flammable, meaning no highly flammable paint insurance or extra equipment for flammable materials is needed. There is a big difference in the classification of water-borne products compared to solvent-borne products—ADR has no regulations for the transportation of water-borne products since they are not flammable.
Both types of metal coatings require specific cleaning products to use once the coatings have dried. One of the main advantages of water-borne products is that when the paint is still wet, you can clean it with water.
Solvent-borne vs. water-borne coatings for metal surfaces
Solvent-borne metal coatings | Water-borne metal coatings | |
---|---|---|
VOCs | Emit high levels of VOCs | Emit low levels of VOCs |
Health & safety | Dangerous to inhale fumes in application and drying process Dangerous when exposed to the skin | Dangerous to inhale fumes during application process (not drying process)
|
Shelf life | Approx. two years | Approx. one year (can be extended by adding chemicals to the formulas) |
Anti-corrosion & weatherability | Depends on the product | Depends on the product |
Application conditions | Forgiving of contaminated surfaces (including traces of dirt or grease) Might only require one layer
| Requires a clean environment and surface
|
Equipment, cleaning & disposal | Highly flammable & require explosion-proof equipment and extra insurance
| Not flammable, no special equipment or extra insurance needed
|
In conclusion
Water-borne coatings aren’t necessarily the right solution for every purpose. This option might be right for you if, for example, your company’s long-term goal is to minimize the negative impact your operations have on the environment. Stricter regulations are most likely coming to the EU, so you might also be preparing for legislation against the use of solvent-borne solutions in your country.
To make the right choice, take the time to consider your goals with metal coatings and understand how water-borne and solvent-borne solutions differ from each other. If you want more detailed advice or recommendations, don’t hesitate to reach out to us. We’re always happy to help you find the best paint and coating solutions for your unique needs.
Keep yourself up-to-date with the latest industrial coatings topics and subscribe to our newsletter.