Different types of industrial wood coatings
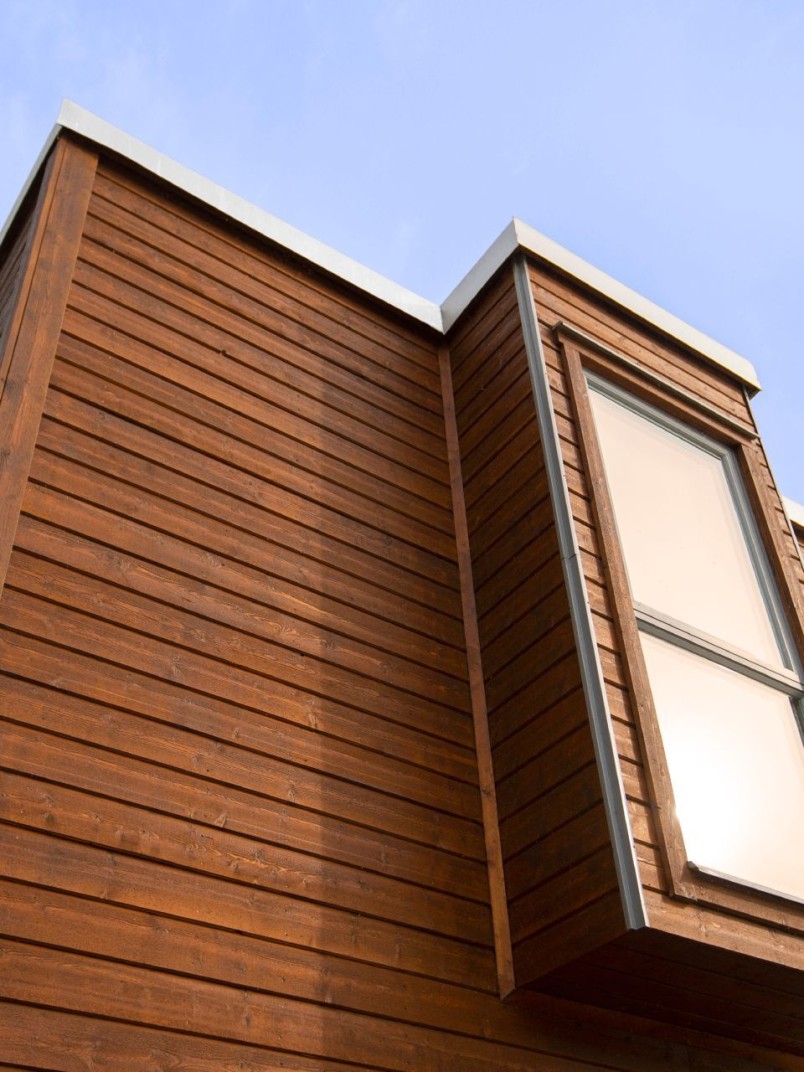
What are the most commonly used wood paints in the industry? Industrial wood paints can be divided into different groups based on their intended purpose of use. Learn what the different kinds of industrial wood paints are and how they should be applied.
Putties
Products that are very thick in terms of their viscosity are commonly called putties. Putties are used for filling the holes, crevices and cracks in raw wood, and for trimming the wood surface. The putty must be easy to apply, filling capacity, and as non-shrinking as possible. Putties can be applied either with a putty knife or capacity using a putty box and either a light or heavy putty machine.
Alkyd resins, nitro cellulose, latex and epoxy and urethane resins can be used as binders for putty. Putties are available in either colourless or white form, or in various brown colors resembling those of different wood species.
Stains
Stains are soluble dyestuffs or pigments or solvents that contain pigments. They are used to stain wood surfaces without covering the structure and pattern of the wood. Due to the low surface tension of stains, a deep and even staining is achieved in most types of wood.
Stains are normally not used alone – instead, one or two layers of lacquer are applied on top. Different shades of stains are available based on our semi-transparent wood stains colour collection.
Both solvent-borne and water-borne stains are available on the market. When choosing the right stains, there are some factors to consider:
- Check whether a current color model is available in order to ascertain whether the resulting shade is correct. Stain color models fade, yellow, or change color due to the passing of time and because of light exposure.
- Wood species and different timber lots affect the final colour of the stain. Check to ensure that the stain used accomplishes the right shade of colour for the wood material used.
- Sanding affects the final shade and appearance of the stain on the wood. A coarser sanding will open the wood’s cell tissue more, enhancing the absorption of the stain into the wood and colouring it more evenly. Sanding too finely may close the wood surface, causing some of the stain to remain wet on top of the wood. This will lead to a blotchy appearance, especially in large items.
- The application method affects the strength of the stain.
- The chosen lacquer type affects the final shade of the stain.
- Stains can be diluted with a solvent, causing the color to become a lighter shade.
- Stains can also be mixed with lacquer, giving the stained surface a more even colour. However, the stain will no longer highlight the differences between spring and summer growth rings. Color differences appearing on unevenly coloured wood can be evened out in the same way.
- A wetting lacquer is the primary choice for use on top of stain.
- The sanding of the sealer is facilitated by the use of stains that cause the substrate to swell as little as possible.
Wood preservatives
Wood preservatives are finishing materials, whose purpose is to protect a wood surface in outdoor use from mould, decay, fungal organisms and bluing. Wood stains ordinarily contain a binder and organic biocides.
A wood preservative should penetrate deep into the wood and prevent it from absorbing excessive moisture. The deeper the active ingredients are made to penetrate, the better they will protect the wood material. In order for the wood preservative to be absorbed as deeply into the wood as possible, the product’s viscosity must be low. A vacuum device can also be used to enhance absorption, the low pressure pushing the wood stain into the wood.
Wood stains may be used in either colourless or colourful form. Tinted wood preservatives contain weatherproof coloured pigments.
Lacquers
Lacquers are finishing materials that form a transparent film as they dry. The wood industry commonly uses acid-catalysed, polyurethane, water-borne and UV-hardening lacquers. The substrate and the structure and form of the item to be coated affect the choice of lacquer and finishing method. Furthermore, the compatibility of the lacquer and wood type must also be taken into consideration, since incompatibility may cause colour disturbances, among other things. For example, acid catalysed lacquer will turn green on palisander.
Pre-treatment, drying and gluing of the substrate also impact on the end result of lacquering. Using thin lacquers, i.e. those with low solids content, produces a result – as the lacquer penetrates into the pores of the wood – that adapts to the form of the wood surface. In open-grained wood, thin lacquer should always be used in order to avoid the formation of air-bubbles. When lacquers with a high solid content, and/or thick layers of lacquer are used, the wood’s surface will easily adopt a “dead” appearance.
Sanding sealers
The most important properties of sanding sealers are easy sanding and quick drying. The wood industry commonly uses one-component sealers that are easy to use and quick to dry. Due to wetting, the wood substrates colors will turn more or less dark depending on the type of lacquer used. This wetting causes the substrate to darken. A stronger wetting of the wood may be desirable when lacquering stained surfaces or dark wood species.
When lacquering light coloured wood species, less wetting is desirable, allowing the wood substrate to remain naturally light. The degree of lightness can be increased by mixing a white titanium-dioxide pigment with the lacquer – this will also reduce the yellowing that results from the impact of UV light.
Top lacquers
The most important properties of top lacquers are mechanical abrasion resistance and chemical resistance. Lacquers suitable for outdoor use must also be weather resistant and able to withstand the dimensional changes of the wood, which means they must be elastic. A similar elasticity is required of lacquers intended for humid conditions.
Paints
Ordinarily, the same raw materials are used in paints as in lacquers. The main difference between the two is that in paints, coloured pigments are used, while in lacquers they are not.
The pigments provide the shade and coverage characteristic of paints. Shades of colour are created in a controlled manner using a tinting machine, tinting formulas, different coloured pigments and base paints. In addition, paints have a better filling capacity; they also protect the substrate more effectively against e.g. UV light. Often, it is mistakenly thought that paint will cover up all defects discovered in the substrate during pre-treatment.
In painting, preparatory work and choosing the right method and paint is a prerequisite for a high-quality end result. There are sealers and top paints, just as there are priming and top lacquers. The most important properties of primers are easy sandability, quick drying and good filling capacity. Correspondingly, the most important properties of top paints are mechanical abrasion resistance and chemical resistance.
Hardeners
Hardeners are substances that are mixed into the paint, producing a hardening reaction. Hardeners can be divided into hardeners and catalysts.
A hardener participates in the drying reaction, forming a film with either the lacquer or the paint. On the other hand, a catalyst only catalyzes, i.e. speeds up the reaction – it does not participate in the reaction itself. In polyurethane and epoxy coatings, a hardener is used as a second component, while in acid catalysed coatings a catalyst is used. In dosing both the hardener and the catalyst, detailed instructions should be closely adhered to in order to obtain a successful result. The amount of hardener required is always calculated individually for each product.
Thinners
Thinners are used primarily for achieving a form for the coating which allows it to be applied on the desired substrate. They are also used to dissolve the binder and give the coating good leveling properties.
Thinners can also be used to affect the wetting of the substrate and to facilitate the formation of a flawless film by adjusting the speed of evaporation. As a result of quick evaporation, the film settles quickly. Slower evaporation allows the film to level off more evenly, but also introduces a greater risk of sagging. In an industrial line, painted products containing slowly evaporating solvents also become more difficult to stack.
The thinner is often chosen bearing in mind the customer line speed and the stacking speed. Thinner is usually a mixture of fast, medium and slow solvents. The dissolving power of the solvent may be limited to one or more types of binder. Thinners are formulated in order to ensure that each coating receives the intended properties. For different paints and lacquers, only the thinner intended for a given paint or lacquer should be used. Most finishing problems occur as a result of unsuitable thinners or their being used in the wrong quantity.
When using thinners, the recommendations mentioned in the product data sheet should be followed. Issues related to the protection of workers and the environment also affect the choice of thinner.
Browse all our products for wood coatings: