ISO 12944 standard and corrosion protection for steel structures
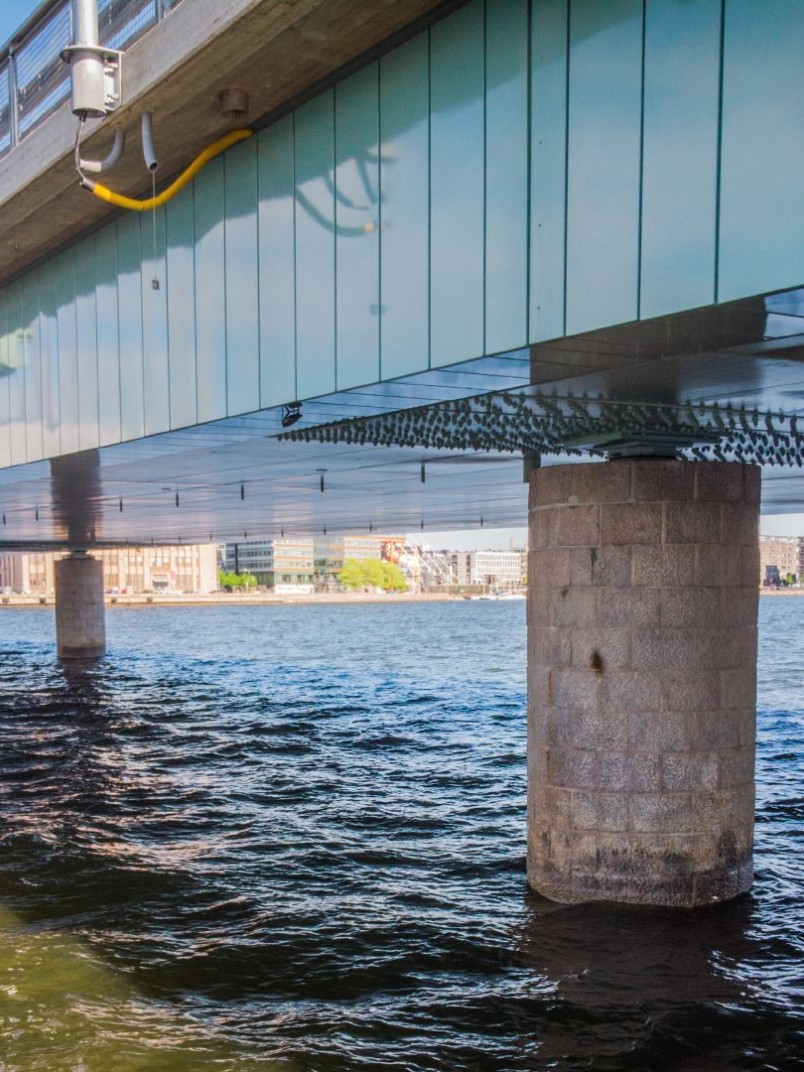
Steel structures have many advantages, but one of the challenges they face is corrosion and how to protect them from it. Steel corrosion refers to the process of moisture and oxygen causing the iron in the steel to oxidise and produce rust which can cause the steel to be more brittle or weaken it, and eventually the steel will disappear without protection. This can result in a shorter lifespan for the steel and high costs/increased costs for unpredicted need of repairing and repainting, hence the desire for an effective preventative process.
ISO 12944 in brief
ISO 12944 is an international standard on corrosion protection of steel structures by protective paint systems. Across nine sections, it addresses all the aspects that influence corrosion in steel and how industrial coatings should be used to prevent or mitigate it.
The standard not only gives information about how to protect the steel from corrosion but also how protection should be designed in different environments and with a defined duration of the protection.
Using the standard in the correct way will help you to design the right protective paint system based on your own requirements.
The standard offers a complete guide to corrosion protection by surface treatment with paint.
It is important to understand that the information in the standard can be either informative or normative. To comply with the standard, the normative information must be followed and used without deviation.
We’ll summarise the most important parts and go into more detail on three of the key areas in the standard; object design, surface preparation and paint systems.
How design impacts corrosion prevention
No matter where a steel structure will be, some aspects are under your control that will impact the effectiveness of corrosion control methods. One of these, the design of how the steel is shaped and used, is addressed in Part 3 of ISO 12944.
In effect, it’s asking you to consider how water and other debris can pool on your structure and how the edges and joints can impact a protective coating.
The below image shows how constant contact with a contaminating liquid can be reduced by considering how the shape and angle allow fluid to drain away or dirt wash off. The red colour shows how dirt or fluid may pool on the structure.
Even with the proper design of the object, a sharp edge on an object is a potential source of system failure that can lead to corrosion.
When a protective coating is applied to a sharp edge the paint film will be much thinner at that point. This creates a potential area of weakness that could fail first since it doesn’t have the specified film thickness.
In this situation, the problem doesn’t lie with the coating product but with the design. This is why it’s important to consider corrosion protection for your steel structures at all stages and not as a final step. The figure below shows how the issues of sharp edges can be addressed in the design stage.
![]()
|
![]()
|
![]()
|
You should also consider the design of welded objects and complicated structures to ensure all the surface area is fully accessible for cleaning, preparation and painting. Any places where this isn’t achieved won’t be protected to the same level as the rest of the object.
Surface preparation for corrosion prevention
Part 4 of ISO 12944 deals with surface types and their preparation for applying a paint protective system. This is crucial since a poorly prepared surface will mean that coating won’t be as effective, and corrosion can occur much earlier than expected. The standard explains and specifies the preparation and to comply with the standard, the normative information must be followed.
Surfaces must be degreased and cleaned of dirt, salts and other contaminants before further preparation or painting. Once cleaned, the surface should be mechanically prepared. It is important to follow the guidance on preparation to get the coating protection performance desired.
The image shows difference after four years between a surface that was degreased and mechanically blasted (top row) and one that was only degreased (bottom row).
Protective Paint Systems
This part of the standard details the types of paint and paint systems used for corrosion protection. You can cross-reference the information in the standard with that provided in a paint’s technical datasheet and system descriptions. This ensures it will deliver the performance required in the location in which it will be used.
The table shows the information that you can get from this standard and where it refers to other sections of ISO 12944.
Protective paint systems
New Work
Refurbishment (Maintenance, repainting): Total & partial
Environment Durability |
C1, C2, C3, C4, C5, Im1, Im2 & Im3 L, M, H, VH |
12994-2 12994-1 |
Environment | CX, Im4 | 12994-9 |
Paint types Primers |
AK, AY, EP, ESI, PUR, PS, PAS & FEVE Zinc Rich = Zn(R), Miscellaneous and Pre-fabrication |
12944-5 |
Surface Substrate preparation |
Carbon steel, HDG steel, Thermally Sprayed Metal | 12944-4 12944-9 |
MNOC: NDFT: |
Minimum Number of Coats (paint layers) Nominal Dry Film Thickness |
12944-5 12944-9 |
Then delving into what this can mean in reference to Tikkurila products, you can see where different steel protective coatings line up as part of the standard in the following table.
ISO 12944-5 Protective paint systems
Paint type | Abbreviation | 1C/2C | Tikkurila Product family |
Alkyd | AK | 1C | Temaprime, Temalac |
Acrylic | AC | 1C | Temacryl, Fontecryl |
Epoxy | EP | 2C | Temacoat, Temabond, Fontecoat |
Ethyl Silicate | ESI | 1C & 2C | Temasil 90 |
Polyuretane | PUR | 1C & 2C | Temadur, Temathane |
Polysiloxane | PS | 1C & 2C | Temasilox |
Polyaspartic | PAS | 2C | Temasolid, Temaspart |
Fluoropolymer | FEVE |
2C |
N/A |
1C = 1 component 2C = 2 components (Base + Hardener) |
There are currently nine sections in total to the standard, with a brief explanation of each below.
ISO 12944-1 - General Introduction
This defines what is covered by the standard, which is specific to corrosion protection properties for paint systems. For example, the structures must be made of carbon steel not less than 3 mm thick, and the paint must be one that dries and cures at ambient temperature.
It also creates a label for a new coating’s durability, explained as the time between the first application and the need for a first major maintenance painting.
Durability | ||
L | Low | Upto 7 years |
M | Medium | 7 - 15 years |
H | High | 15 - 25 years |
VH | Very high | More than 25 years |
ISO 12944-2 - Classifications of environments
The environment around a steel structure will play a huge part in determining the corrosion rate, and this creates a standard language to label the different possibilities.
Raiting for atmospheric corrosivity categories |
C1 |
C2 |
C3 |
C4 |
C5 |
CX |
Raiting for immersed corrosivity categories |
Im1 Fresh water |
Im2 Sea or brackish water |
Im 3 Soil |
Im 4 Sea or brackish water with cathodic protection (offshore structures) |
ISO 12944-3 - Design considerations
This has already been covered above, but, in essence, it deals with the basic criteria for the design of steel structures to be coated by protective paint systems.
ISO 12944-4 - Types of surface and surface preparations
There is more detail on this further up. However, in brief, it describes the surfaces and their preparation before painting.
ISO 12944-5 - Protective paint systems
Also already explained in more detail, it describes the types of paint and paint systems commonly used for corrosion protection.
ISO 12944-6 - Laboratory performance test methods
This section of the standard details the laboratory test regimes, so coatings have a common way they are checked for comparison purposes and qualification. It’s most often used by research and development teams.
ISO 12944-7 - Execution and supervision of paint work
Detailing how paints should be applied and how to control the result, this section gives guidance on everything from initial work to follow-up inspections.
ISO 12944-8 - Development of specifications for new work and maintenance
The standard contains several templates for reports, project specifications, flow charts, checklists, final reports on paint work and so forth. It can prove a useful reference when creating documentation for specifications and inspections.
ISO 12944-9 - Protective paint systems and laboratory performance test methods for offshore and related structures
The standard details both the system description and laboratory testing for paint systems intended for steel structures exposed to a severely corrosive environment, for example, offshore. This refers to those labelled as CX or lm 4 under section ISO 12944-2.
Who is ISO 12944 for?
The standard is relevant for a broad range of roles since it covers everything from the design stage of the steel structure to post-coating application inspections.
Whether engineer, coating professional, general manager or something else, if you are involved in the production chain of steel structures that need corrosion protection, then at least part of ISO 12944 will be an essential reference point for you.
Changes to ISO 12944
The last update to the standard was in 2019, but that doesn’t mean there won’t be future changes. Keep tracking it and keep communication lines with your coatings supplier open since they can also give you information on any changes and how they impact their products.
How to find the suitable paint system?
Tikkurila supplies materials and paint systems which are compliant with ISO 12944. We have collected our coatings into easy-to-use paint systems, which make it easy for you to find the right combination of treatments for your project.