Application methods for industrial wood coatings
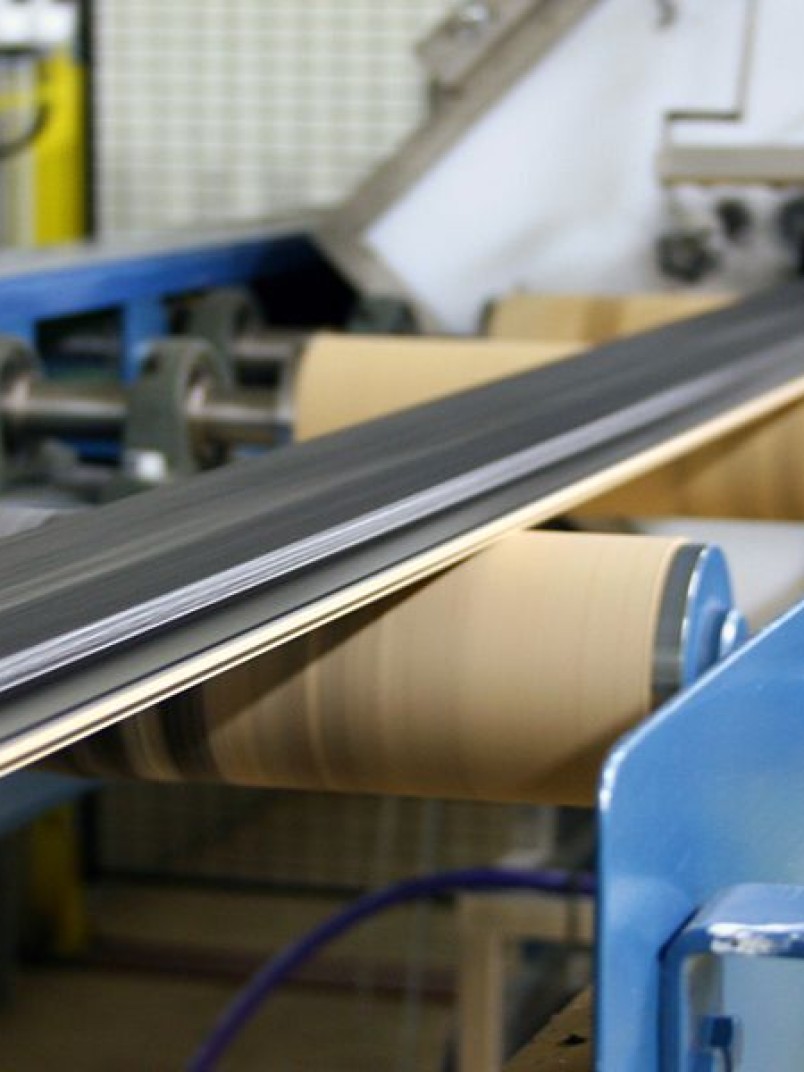
There are many possible ways to apply wood coatings in a production line, and no single method is useful in every situation. Different product types require different ways to apply wood paint to achieve the desired outcome. Understanding the differences between the different application methods and where each is most advantageous can help decision making when planning future developments.
The challenge and opportunity come when expanding into a new wood products area, updating a production line or changing the wood coatings used. This applies no matter what types of wood coating you are using. What is being painted and in what volume will dictate a lot of the decision. Is the current line adaptable? Are there ways to optimise the current method?
The factory and the floor area available for the coatings line will also impact the choice since there must be enough space available. A whole new building would be an even bigger project for your industrial wood products and coatings!
Types of wood coating equipment
This isn’t an exhaustive list as there are other options, but this covers the main choices available to those looking to coat wood on an industrial scale.
Airless spraying
In airless spraying, the coating is dispersed by using significant differences in pressure levels to press the coating through the small opening in the nozzle as a mist.
This method allows you to apply high volumes of coating easily. However, some types of paint sag easily and the spray gun can’t be used to adjust the shape.
Air-assisted airless spraying
In air-assisted airless spraying, high-pressure and conventional spraying is used to create a fan application.
As with airless spraying, this allows you to apply high volumes, but it is enhanced because you can easily adjust the shape of the spray fan. It may also be a little more efficient, but, more than that, the paint film will look smoother, and the levelling is superior.
Electrostatic spraying
Electrostatic spraying utilizes the electrostatic field that forms between two objects of different voltage levels to apply a coating.
The main benefit of this is that the overspray loss is quite small, so you can save by using a smaller volume of paint. However, the trade-off is the cost of the equipment can be high.
Two-component spraying
This mixes hardener and paint in the correct quantities before applying them with a spray gun. If you’re using fast-drying two-component coatings, it will allow you to complete the application within the timescales required by the different coats.
This removes the need for any manual mixing, which helps when the pot life of a coating is short. Moreover, it also ensures that the mixing ratio between the two products is always correct.
Automatic spraying
If you’re dealing with a large number of similar objects, then automatic spraying of the wood coating can prove beneficial. There are different types of equipment options for this, linear, traverse and carousel being some, but the key here is ensuring that the equipment is reliable.
This equipment will produce an even quality finish for your products and operate quickly for higher volumes.
Robot spraying
This equipment setup will consistently produce the same motions time and again, meaning you can be confident in what is applied.
Robot spraying makes it possible to spray multi-shape objects and achieve the same level of quality. For example, a chair is very complicated to paint due to the legs etc. The robot will finish it in the same way every time. However, the robot must spray the same amount of paint at all times.
Methods of applying industrial wood coatings
In addition to different types of equipment, there are also different approaches possible for the method of applying wood paint. Once again, this isn’t a list of every option but instead a summary of the most relevant for industrial wood coatings.
Curtain coating
By allowing the object to go through a wall or ‘curtain’ of paint, a layer is applied to the product.
This can result in fast production speed and minimal waste since the paint is circulating in the system.
Vacuum coating
The first thing to note here is that this method is only suitable for water-borne coatings. An even paint mist is applied to all parts of the product inside a coating chamber.
This is another fast method that has minimal wasted paint. It’s proving to be quite popular in some industry sectors, for example, with exterior cladding painting companies.
Roller coating application
When dealing with large quantities of flat surfaces, roller coating is an option where the paint is pumped in between the dosing roller and the spreading roller.
This can result in a very fast painting method, although the limitation of only applying to flat products, like doors or kitchen cabinets, means it isn’t suitable for everyone.
Dipping
Products are simply dipped in the dipping basin either
in parts or assembled. For example, parts of a window can be primed this way.
It isn’t one of the most commonly used methods, but it can be an option to consider in specific circumstances.