Industrial wood coatings for different production lines
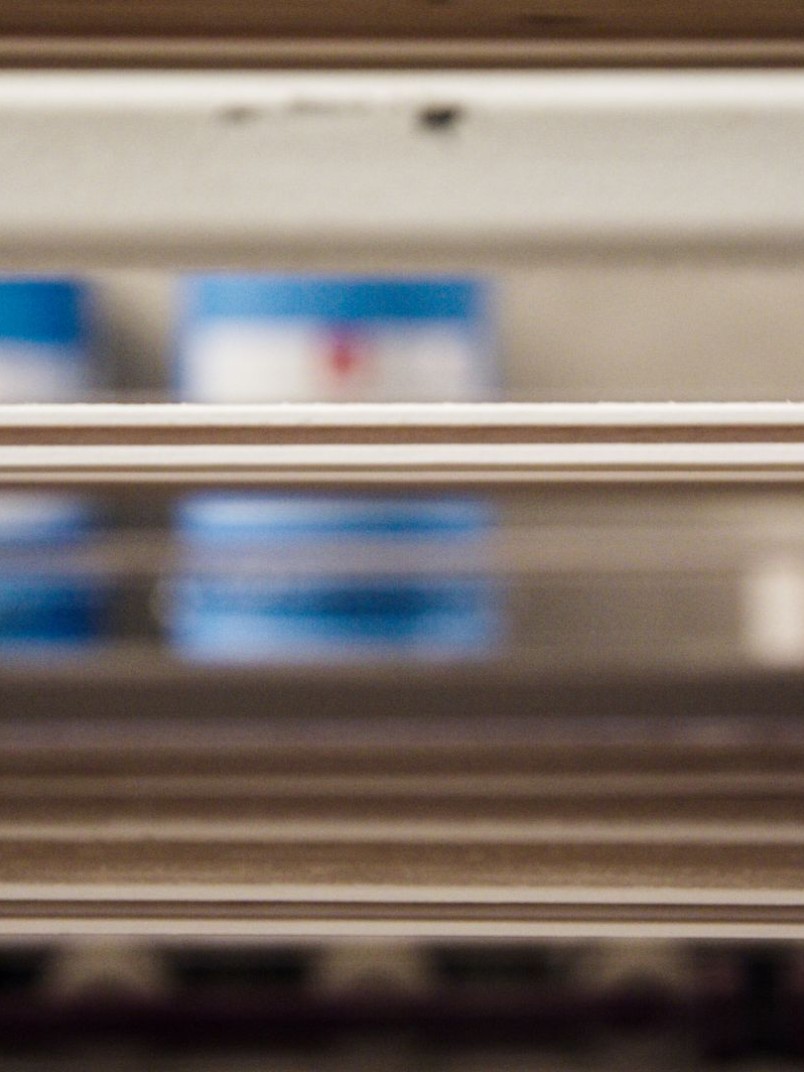
Finding the right wood coating for an industrial production line results in a more efficient application process and saves time and money for the business. This aspect can be sometimes forgotten especially if there is a well-established industrial wood paint in use and coating process in place.
However, there is an opportunity in reviewing what’s in use to ensure it’s the best option and recognize what can work best in different production lines. This is particularly crucial when expanding into a new area or updating equipment.
Not all production lines are the same, which will influence the type of wood coating you use. The first step is understanding the difference between water-borne and solvent-borne coatings and the impact this has on the production line for your industrial wood products.
Water-borne vs solvent-borne wood coatings
Solvent-borne wood coatings are still the predominant choice in the market. Still, water-borne coatings do have an established presence, and more regulations and demands around sustainability are pushing this further. Is it a simple switch, though, and what should you consider in terms of your production line?
There is spraying equipment that can be suitable for both water-borne and solvent-borne coatings, but many things can affect this. For example, sometimes older equipment may only be suitable for applying solvent-borne since paint residues can cause problems.
The result produced by the different coating types may impact the choice made. However, the first step is to discuss the coating with your coatings partner so they can advise if it is compatible with your equipment. They can guide you through the different options to discover the right blend of paint type and finish that is suitable for your equipment.
Whether you are using paint or lacquer doesn’t impact your production line as they can be applied from the same line. However, if multiple production lines are available, sometimes they are separated out. Find out more about the different types of industrial wood coatings.
Changing your painting line
Making changes to an industrial wood coatings line is typically a big investment, so it’s vital to understand what paints you intend to use and how they may impact your choice of equipment.
Your coating equipment supplier will be the core of most of these conversations. Still, by including your paints supplier in the discussions, you can ensure that the products you wish to use are suitable for a new painting line.
Even if you’re looking to optimise your current production with your current coating line, a visit from your paint supplier can help see which paints are suitable to deliver the right quality. You can then select the best candidate based on your current or new line.
The importance of drying times
Changing wood coating can seem like a big undertaking, especially when you have a well-established process that has been working for years. It may feel hard to get the choice right when selecting which to proceed with on a new range of products. One of the most important things to consider concerning your wood coating production line is the drying time.
If, for example, your production line has a sixty-minute drying time that can’t change, that may limit your options since you must select a product that dries in that time. This is a key element and a place where your choice of equipment and coating intersect.
There can be an advantage in using a higher solid content wood coating in these situations. It can result in faster drying products within the same production line, and when considered in respect of the overall price of the application, end up being more cost-effective.
Factoring in the drying time and how it applies to your production line is crucial to the overall efficiency and so it’s importance when selecting a wood coating can’t be understated.
Working with your industrial wood paint supplier
Close cooperation with your paint supplier can pay serious dividends. By understanding your needs and production line, they will be able to recommend which product will produce the best results, both in terms of suitability for your production line and in terms of production efficiency.
There is no simple chart you can refer to that will immediately give you all the answers. It may even require a special formulation created to suit your painting line to get the drying time and product viscosity correct.
Aureskoski Jalostetehdas delivered the wooden slats for the Helsinki Olympic Stadium canopy and required a new shade with specific properties that could work with an increased production capacity. In this case, by working with Tikkurila, they were able to identify all the product needs and ensure the new coating could be applied at the rate needed to meet their demanding schedule.
The future of wood coatings
There has long been discussion about water-borne wood coatings and water-borne UV products as the future, and therefore, production lines should begin to adapt to that trend. However, the reality is this will not be applicable in all cases.
It seems probable that cladding manufacturers are likely to end up working mostly with water-borne products on their production lines, but, for example, kitchen cabinets and furniture products may remain solvent-borne.
Overall, production lines are all individual with specific demands to that company. There’s no way to say do this or do that immediately, but efficiencies and improvements can be made that will save time and money. Identifying the right industrial wood coating for your products and coating line is best done by working closely with a coating supplier. They can advise and recommend options available to you based on their in-depth knowledge of coatings, helping you reap the benefits.